Welcome Message
Welcome to the Department of Mechanical Engineering at IIT Kanpur. We started our journey in the year of 1960. Over the last six decades, we have grown our expertise and competence in the core Mechanical Engineering curriculum and research....
- Read More
-Prof. Ashish Dutta
Head, Department of Mechanical Engineering
Featured Faculty
Research covers all aspects of dynamics and vibration, nonlinear dynamics, rotor dynamics, continuum and granular mechanics, plastic instability, robotics, intelligent control systems, microsensors and actuators, CAD, machine dynamics, smart structures, active and passive vibration control, composite materials, non-destructive testing, finite element method, multiscale modelling of solids, acoustics and noise control, mechanics of fracture, functionally graded composites, mechanics of biological membranes, mechanics of nanomaterials, mechanical behaviour of polymers.
The entire research in Solid Mechanics and Design stream is divided into the following Three tracks.
Research facilities
Applied Solid Mechanics | Computing facility |
Compliant and Robotics Systems (CARS) Lab | Compliant Mechanisms and Robotic Systems |
Computational Mechanics Group | 3 large clusters |
NDT Lab | USIP-12 Omniscan Phased Array, Power Laser Nd-Yag, Heterodyne He-Ne Detector |
Nonlinear Mechanics Lab | Shaker, Accelerometers, Force Transducers |
Smart Materials, Structures & Systems Laboratory | 3D Laser Doppler Vibrometer, dSpace ACE 1103, 1104, Multi channel SMA amplifiers, d33 meter, Magnetic Levitation Control |
Our department's research is divided into the following major areas although interdisciplinary research and sharing of expertise amongst groups within the department and institute is commonplace.
More information on expertise of our faculty and staff, primary research focal areas, and major research centres could be found by following the links given below. Further details are provided on the specific websites of individual research groups and faculty members. For additional information, download the department brochure.
Dropwise condensation is a heterogeneous phase-change process in which vapor condenses in the form of discrete liquid drops on or underneath a cold substrate.
The heat transfer coefficient of dropwise condensation can be up to an order higher than film condensation and mixed-mode condensation, particularly with low conductivity liquids. Therefore, it is of considerable interest in application such as thermal power plants and condensing equipment. It is also of interest in the material enrichment of large molecular weight liquids. Dropwise condensation is complex process, involving drop formation at the atomic scale, growth of drops by direct condensation, coalescence of drops, drop instability and movement, followed by fresh nucleation. Hence, the dropwise condensation process is hierarchical in the sense that it occurs a wide range of length and timescales. In addition, it depends on the thermo-physical properties of the condensing fluid, physico-chemical and thermal properties of the cold substrate, orientation of the cold substrate, surface texture, degree of sub-cooling, thermodynamic saturation conditions and presence of non-condensable gases. As the driving temperature difference for the process is very small, experimental measurement of heat transfer coefficient in dropwise condensation is a challenging task.
Against this background, a mathematical model of dropwise condensation process underneath an inclined surface is presented in this monograph. The model includes formation of drops at the atomic scale, growth by direct condensation, coalescence, gravitational instability including slide-off and fall-off, followed by fresh nucleation of liquid droplets. The stability criterion is developed as a force balance equation at the level of a drop. Transport parameters of a sliding drop are determined using a CFD model and presented in the form of correlations. Performing the simulation of the complete cycle of dropwise condensation, the spatio-temporal distribution of drops is obtained. Consequently, quantities such as instantaneous condensation pattern, area of coverage, wall friction, and heat transfer rates, as well as important time and area- averaged wall heat fluxes are determined. The simulated condensation patterns are compared against experimentally recorded images. The model is also validated against wall heat fluxes reported in the literature. While applicable for a wide range of fluids such as water and liquid metals, the model is seen to be sensitive to surface texture, inclination, and saturation conditions.
Work is continuing on understanding droplet coalescence on textured surfaces, droplet formation and coalescence of liquid metals and thermo-hydrodynamics of three-phase contact line motion.
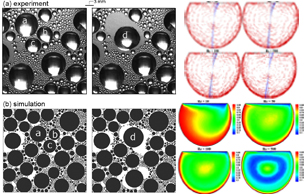
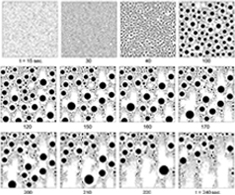
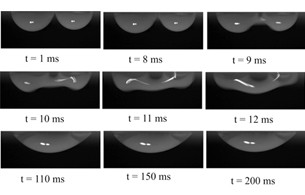
![]() |
|
![]() |
|
![]() |
|
![]() |
|
![]() |
|
A team of researchers at Indian Institute of Technology Kanpur have designed and experimentally evaluated a new 8-DOF biped robot with compliant shanks .
In this work the shanks of an 8 DOF rigid link biped robot are replaced by compliant links that deforms as the robot walks. The Dynamic equations of motion of the biped are derived using the Euler-Lagrange method and the work done for both the rigid and compliant link biped are compared, to study the effect of compliance. By varying the thickness and shape of the compliant link and other gait parameters, various gait trajectories are optimized based on the work done and balance. The designed biped robot was experimentally evaluated for following the optimal gait pattern. The application of this new design would be in soft robots that are safe for interaction with humans. This research was carried out by Abhishek Sharkar (PhD student) and Prof. Ashish Dutta (Professor) in the Department of Mechanical Engineering and has been published in Robotics and Autonomous Systems, 2015.

CAD Model of rigid link biped

Rigid link replaced with compliant shank

Optimal gait

Balance during gait
Highlights
- List of candidates from CFTI selected for provisional admission for PhD program in Mechanical Engineering for the session 2025-26-I.New
- Department of Mechanical Engineering, IIT Kanpur Presents 2nd Mechanical Sciences Young Investigators Meet MSYIM 2025 17-19 March 2025. Visit the website for more details: MSYIM 2025
- Guidelines for the Application of Institute Post Doctoral Fellows
- Applications invited for direct PhD students for the semester 2025-26-I. Last date of application February 20, 2025
- List of Selected candidates: Winter PG Admission 2024
- Candidates Shortlisted for Interview: Winter Admission PhD Programme 2024
- Dates for PhD winter admission 2024 written exam and interviews: November 27-28, 2024
- Reporting date of all new PG students: Jul 18 - 19, 2024
- Departmental Orientation of new PG Students: Jul 20, 2024, 2:30 PM onward, Venue: L16
- PhD admission (Round 2): Application form available here. Last date of application: 4th July 2024. Online written test: 7th July, 2024, Online/Offline Interviews: 10th July, 2024
- M.Tech. Admission (through COAP): Cutoff score, Vacancy and fee paid data
- Selected candidates for provisional admission in PhD programme
- Selected and WL candidates for MS(R) admission (Institute-sponsored category) Round 1
- Rolling advertisement for faculty recruitment